Bosch Invests Millions in Cutting-Edge Metal 3D Printing Facility
Bosch Invests Millions in Cutting-Edge Metal 3D Printing Facility
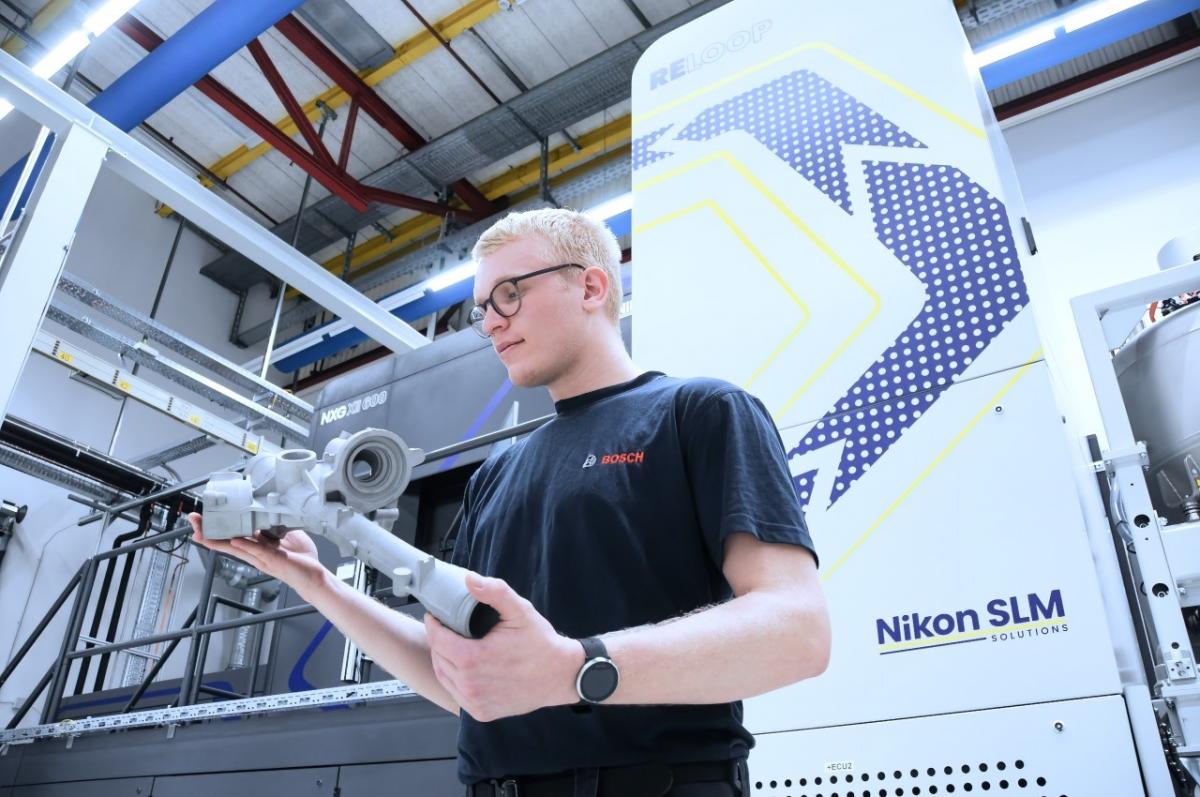
Setting new standards in large-scale and volume production, Bosch invests almost six million euros in a metal 3D printing center. Bosch is the first European Tier-1 supplier to have a facility in this performance class. Plans for volume production of highly complex shapes, from housings to engine blocks.
Bosch is elevating the manufacturing of metal components to new heights, focusing on speed, precision, flexibility, and energy efficiency. With the addition of a cutting-edge metal 3D printer at its Nuremberg facility, Bosch is enhancing its role as an industry leader in advanced manufacturing. The facility, which represents an investment of almost six million euros, positions Bosch as the first European Tier-1 supplier to operate a 3D printing facility of this caliber. The investment includes acquiring a Nikon SLM Solutions NXG XII 600 metal 3D printer.
“Bosch is fully committed to investing in Germany as a production hub, introducing innovative technologies that unlock significant sales potential,” says Klaus Mäder, a member of the Bosch Mobility sector board overseeing operations worldwide. The new 3D printer is designed to expedite the production of metal parts, which are traditionally slow to manufacture using conventional methods. Alexander Weichsel, the commercial plant manager at Nuremberg, explains, “This facility will make metal part production faster and more efficient, enhancing our competitiveness.” The technical plant manager, Jörg Luntz, adds, “We are setting a new benchmark in metal 3D printing. This technology opens a world of possibilities for large-scale production.”
From hydrogen components and motor housings for electric vehicles to engine blocks for racing cars, the capabilities of Bosch’s new facility are vast. Its twelve lasers melt metal powder layer by layer using a design file to form complex structures. The new system is up to five times faster than previous 3D printers, enabling the production of intricate designs that would be impossible with traditional milling techniques. The ability to 3D print curved channels and create parts without extensive tooling dramatically reduces material waste, increasing flexibility and sustainability in production.
One particularly exciting application is engine block manufacturing. Traditional methods take up to three years from concept to volume production, with mold creation alone taking 18 months. However, with 3D printing, the process is significantly streamlined. The design data is sent directly to the printer, bypassing the need for molds, and a complete engine block can be printed in just a few days.
At full capacity, the new facility can produce 10,000 kilograms of metal components annually, operating at speeds of 1,000 cubic centimeters per hour. This leap in production speed is intended to reduce time-to-market for Bosch’s customers drastically. “We aim to outpace traditional manufacturing and bring products to market faster using this technology,” Luntz emphasizes. “Bosch is already a leader in industrial-scale technology, and with this step, we are pushing the boundaries of what’s possible with metal 3D printing.”
This breakthrough in volume production will benefit the automotive industry and open up new opportunities in sectors such as energy and aviation.
Bosch 3D Printing
Metal 3D Printing
Automotive Manufacturing
Advanced Manufacturing
Additive Manufacturing
-
World Architecture Festival (WAF) 2025
November 12, 2025 8:00 AM
-
Senior Software Engineer - Virtual Machine and Container
Bengaluru, Karnataka, India
Microsoft Office