Europe's most advanced special profiling line goes into operation at voestalpine in Krems
Europe's most advanced special profiling line goes into operation at voestalpine in Krems
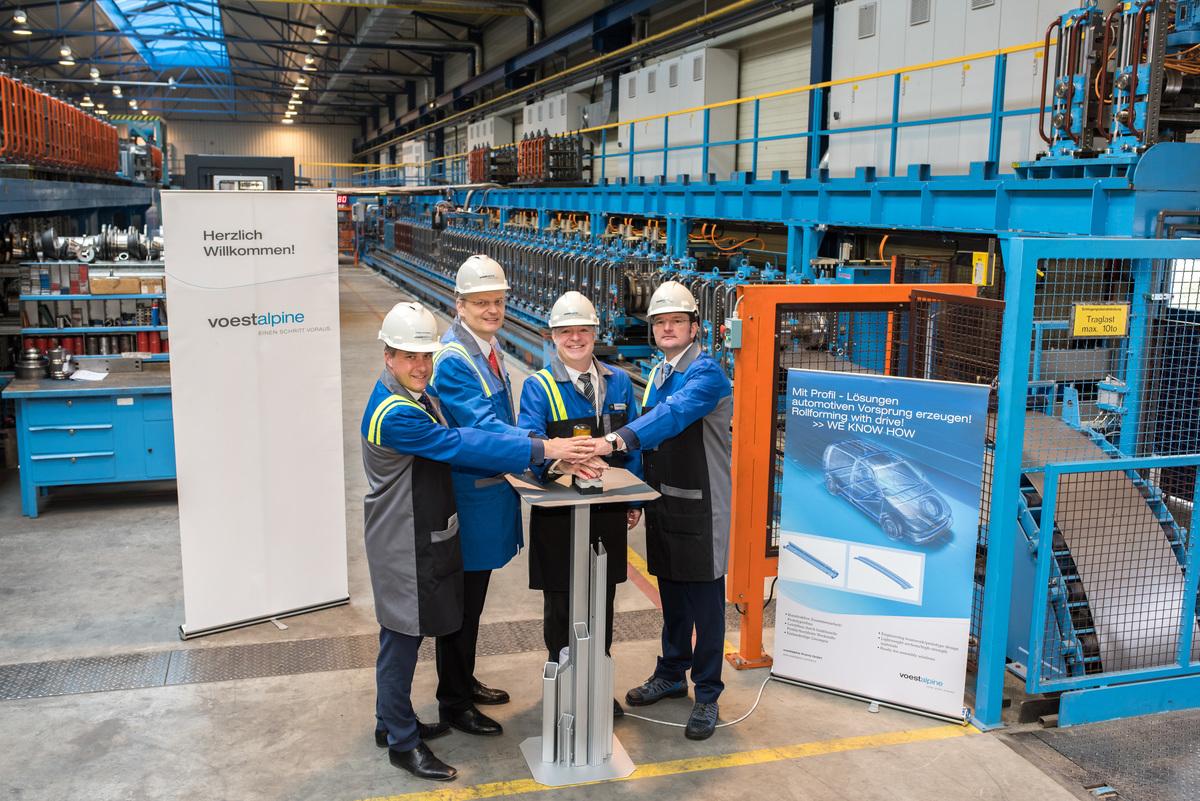
It will produce highly-complex special tubes and sections for customers in sectors including the automotive and commercial vehicles industries.
voestalpine has invested over five million euros in the new line, strengthening its position as the global market leader in the production of top quality complex, cold-rolled steel tubes and sections.
Lower Austria is a key Austrian province for the global technology and capital goods group voestalpine. Around 2,300 employees work here at a total of seven production companies across all four Group divisions, generating total revenue of almost EUR 560 million in the business year 2014/15. In Krems, where the globally active voestalpine Metal Forming Division, headed by Dr. Peter Schwab, is headquartered, Europe's most advanced special profiling line is going into operation.
“We drew on the decades of experience we enjoy here at Krems when developing the new profiling line. By putting the most advanced line of its type in Europe into operation, we are setting another milestone in the growth area of mobility,” says Schwab.
The profiling line at voestalpine Krems GmbH will be used to manufacture products including double laser welded special tubes for the commercial vehicles industry, and welded special tubes for the automotive industry. It can also be used to complete orders with complex and variable hole patterns for the construction industry.
Intelligent drive technology meets energy-saving hydraulics
The innovative special profiling line runs with new and intelligent drive technology, the product of voestalpine Krems's decades of technical know-how. The new technology spreads the drive torque in order to prevent the steel strip slipping. This results in an even higher quality product. The modern line is also driven using special energy-saving hydraulics.
This ensures the profiling line only runs at full power when actually necessary, otherwise standby mode is activated. This innovative approach, together with the intelligent drive system, enables up to 1 million kWh of electricity to be saved each year–equivalent to the annual energy consumption of around 300 households, or roughly 176 tons of CO2.
Capacity utilization at Krems guaranteed
The special profiling line is not only designed for processing new dimensions: when necessary, products on existing lines can be diverted to the new line in order to relieve production bottlenecks. Permanent two-shift utilization of the line is already ensured, and three-shift operation is already planned to meet major upcoming orders. voestalpine has created numerous product highlights at Krems to date. They include steel tubes and sections for intelligent and statically-optimized substructure components in photovoltaic and solar installations, innovative system solutions for orchards and viticulture, and modern, advanced profile systems for a variety of door and portal constructions.
The two voestalpine plants, voestalpine Krems GmbH and voestalpine Krems Finaltechnik GmbH, currently have more than 800 employees. Krems is also an important training center for skilled workers; the 1000th apprentice started his training at voestalpine in Krems in September 2015. Currently 49 apprentices are being trained as production and process technicians, metal and mechanical technicians, and electricians.
Metal Forming Division
The Metal Forming Division of the voestalpine AG achieved a total sales volume during 2014/15 of 2.3 billion and an operating result (EBITDA) of 331 million euros. The division employs roughly 10,500 staff members and does business with almost all European car manufacturers. Within the Group, it constitutes the center of competence for highly refined sections, tubes, and precision steel strip products as well as ready-to-install components made of pressed, stamped, and roll-formed parts in steel and in aluminum, with a focus on the automotive industry.
Its combination of material expertise and processing competence is unparalleled throughout the industry, and its global presence makes the division the preferred partner to customers who are looking for innovativeness and quality.